Investing in the right heavy-duty metal shredder is pivotal for industries dedicated to metal recycling and waste management. These powerful machines are designed to transform bulky metal scrap into manageable, valuable pieces, ensuring both economic and environmental benefits. Understanding the nuances of these shredders can significantly impact operational efficiency and productivity.

Choosing a heavy-duty metal shredder depends on multiple factors that align with specific industrial needs. It begins with the machine's capacity. High-capacity shredders are essential for operations dealing with substantial volumes of metal scrap. They offer robust performance by shredding large quantities without frequent downtime, thereby maximizing throughput and minimizing costs.
Material compatibility presents another critical consideration. Different metals, such as aluminum, steel, copper, and alloys, require machines capable of adjusting to varied material properties. High-torque, low-speed shredding technology is vital for efficiently processing tough, dense materials without premature wear or damage to the machine. Selecting a shredder tailored to specific metals can prevent bottlenecks and boost overall workflow efficiency.
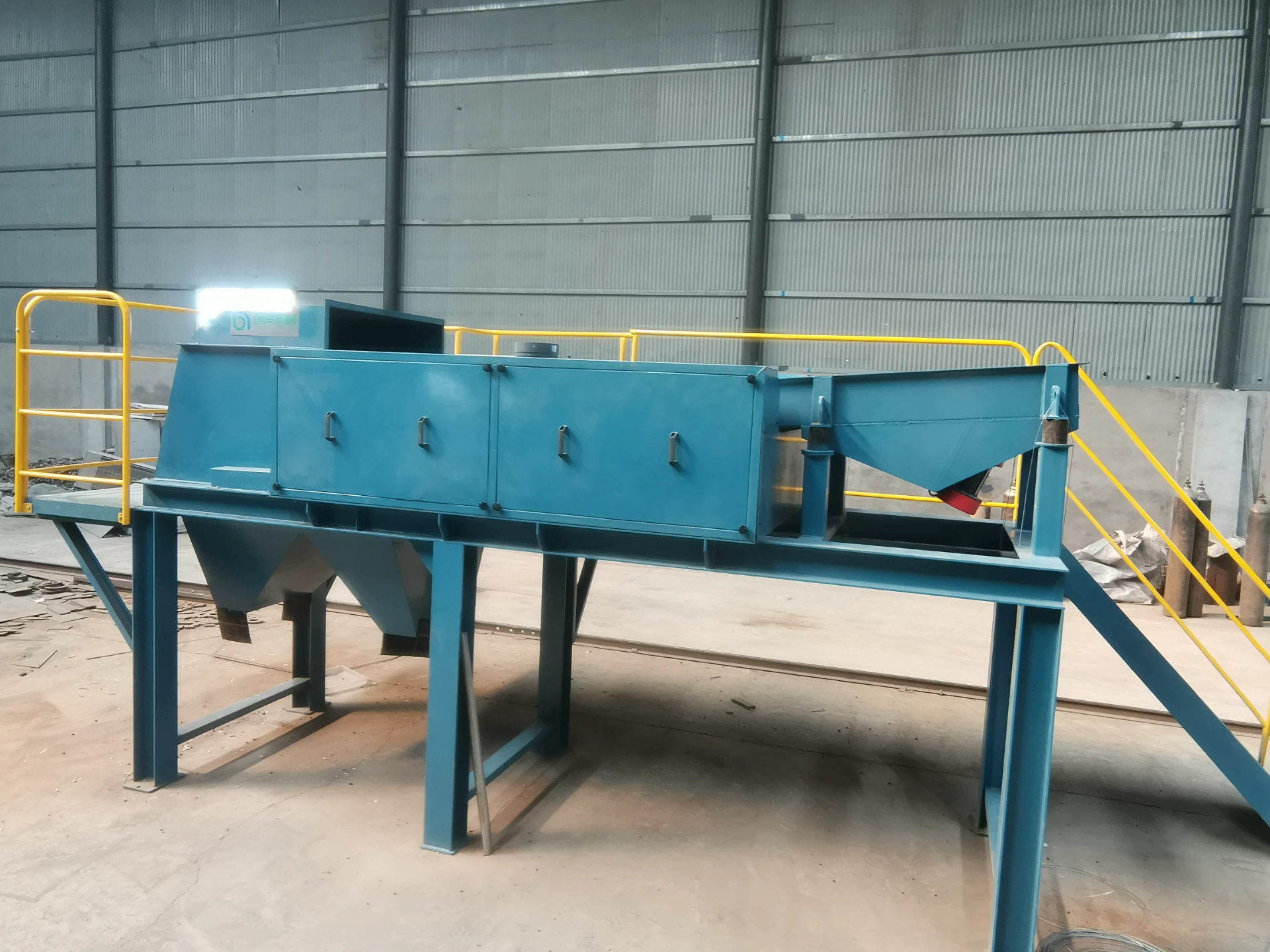
The role of cutting technology is often underemphasized but contributes significantly to the shredding process. Precision-engineered, hardened steel blades ensure longevity and consistent performance by withstanding the rigors of heavy-duty shredding. The right blade design also influences the particle size of the shredded output, critical for downstream processing or sale in the recycling market. Maintaining blade sharpness and regular maintenance is paramount to ensuring optimal shredder performance.
Automated features and control systems in metal shredders enhance both safety and usability. Advanced models incorporate smart technology with user-friendly interfaces, offering real-time monitoring and diagnostic capabilities. Automated feedback systems can adjust operations dynamically, compensating for inconsistencies in feed material and optimizing energy consumption. These features not only increase safety by reducing human interaction but also enhance machine efficiency and reduce operational costs.
heavy duty metal shredder
Durability and ease of maintenance further dictate the choice of a heavy-duty metal shredder. Machines constructed from high-grade steel and reinforced components can withstand harsh working environments, thereby extending service life. Easy access to parts for routine maintenance or unforeseen repairs is equally important—choosing a design that allows quick blade changes and easy cleaning reduces downtime significantly. Thus, comprehensive support from manufacturers and availability of replacement parts are essential considerations.
Economic feasibility is a decisive factor in selecting shredders, balancing upfront costs against long-term benefits. Though heavy-duty shredders may entail a higher initial investment, their enhanced efficiency, energy savings, and reduced labor costs justify the expense. Many firms find that over time, these machines provide a higher return on investment through increased recycling rates and operational savings.
Safety features must never be overlooked. Consideration of compliance with industry safety standards is essential in protecting employees and maintaining trustworthiness in operations. Machines equipped with emergency stop mechanisms, protective guarding, and automated monitoring systems mitigate risk and ensure a safer working environment.
The heavy-duty metal shredder market is continually evolving with technological advancements. Staying abreast of these developments can make a tangible difference in operational outcomes. Current innovations focus on enhancing shredder efficiency through AI integration, optimizing energy use, and reducing carbon footprints. Future-oriented companies can differentiate themselves by investing in machines offering such innovative solutions.
To wrap up, a strategic approach to selecting heavy-duty metal shredders involves a comprehensive evaluation of capacity, material compatibility, cutting technology, ease of maintenance, safety, and economic factors. The right machine not only enhances recycling efficiencies but also contributes positively to sustainability efforts. As global demand for metal recycling grows, companies equipped with state-of-the-art shredders will undoubtedly lead in productivity and environmental responsibility.